An Inside Look: Company Visits in the Operations Immersion
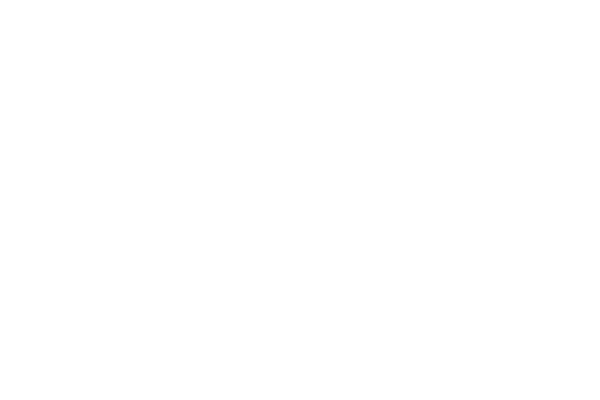
by Shigeki Abe, MBA ’13
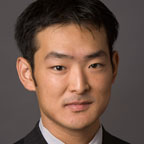
Taking the Strategic Operations Immersion has been one the most memorable and valuable experiences I’ve had while at Johnson. During the spring semester last academic year, in combination with rigorous coursework, we went on five trips visiting more than a dozen companies in total. The trips varied in length, from one to five days, and the companies we visited were diverse. We visited a semi-conductor manufacturer, a hospital, and an acoustic instrument producer, to name a few. We also topped off the semester with a noteworthy week-long Kaizen project at one of the company’s sites. Stemming from the Japanese philosophy of engaging in continuous improvement, Kaizen events encourage employees to develop ways of improving their business responsibilities and processes. The ultimate goal is to eliminate waste and provide immediate benefits to problems.
My favorite trip, though, was to Martin Guitar, a legendary guitar maker who has been producing some of the best guitars in the world since 1833. The company’s clientele has included famous musical artists such as Johnny Cash and Elvis. It was great to see how the company has been able to adapt with changing needs and demands but still maintain its culture, quality of craftsmanship, and innovation.
We participated in a candid conversation with management on how the company has differentiated itself from its competitors, while still being able to grow its customer base and profits. This conversation was eye-opening and valuable for many reasons, but one thing stands out in my mind: We had the opportunity to hear about Martin’s decision-making process when it decided to outsource some of its production.
Often, when we hear the words “outsourcing” and “offshoring,” we immediately think about low-paid workers with low quality of life. However, we learned that Martin’s approach to outsourcing was very different in that it was very selective about where to go and whom to approach. It ultimately decided it wanted its outsourcing partner to mirror its headquarters’ employee-focused culture by paying premium salaries, investing in employee development, and retaining its music-centric atmosphere to spur innovation.
Contrary to what some may think, we don’t just visit manufacturing companies and focus strictly on operations in this immersion. This offering has a great mix of service and manufacturing companies, and we get a chance to meet a wide-range of professionals. One moment we were talking about firm-wide strategies with a company CEO, while the next moment we were talking about employee-retention and company culture with the head of HR. And at other times we were talking about improving inefficiencies with the COO and getting key inputs from line-workers.
It was beneficial to see how different companies manage day-to-day operations and tackle the challenges of running a business. But what was truly stunning to me is that no matter how different the companies or industries are, there are commonalities between them all.